- Blog Procurement Management
- 03 Nov 2022
Procurement: The Post-Order Phase
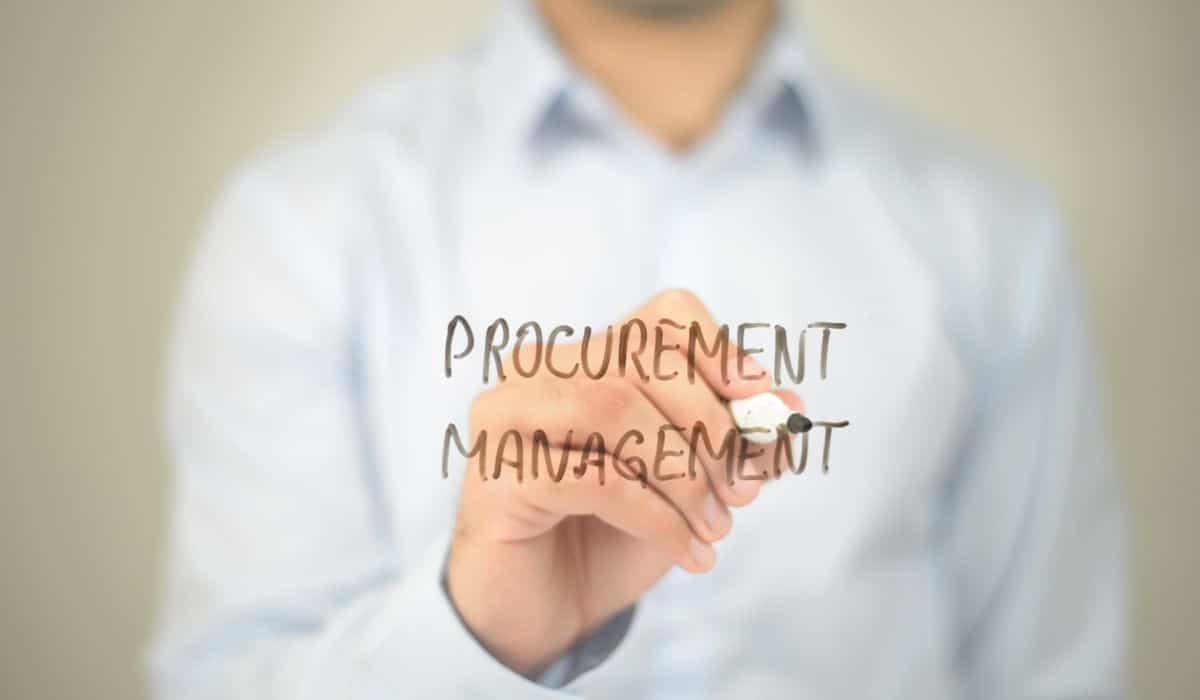
In a previous blog post titled “How Procurement Delays Hold Up Project Completion” we looked at some of the challenges that can occur during the procurement processes of the pre-order phase. However, such challenges are not confined to the pre-order phase.
“Procurement, if done right, is like half the project done right”.
This statement came from my experience of a project where the procurement of an AHU got impacted due to a hitch at the manufacturers’ end even though the tendering, design, technical approval, and even the delivery was on track. What happened is that after the delivery of the AHU to the site, it was noticed that UV filters had not been delivered despite all the details being mentioned in the approved shop drawings and technical specs. While scrutinizing the process post-approval, it came to the notice of the project team that the requirement of UV filters had not been updated in the manufacturers’ internal system. So, all the ducting works were completed, and the connections with AHU was the only pending task for testing and commissioning of the entire HVAC system. Finally, the manufacturer admitted their mistake and agreed to supply the filters in 4 weeks, but the whole project was delayed, and the inauguration of the office had to be postponed by 4 weeks. It is worth noting that there was no penalty levied on the manufacturer in this instance as there were other internal reasons holding up the inauguration. But that’s not the case always, as a manufacturer or contractor can easily face stiff penalties for such delays.
To avoid the situations mentioned, inspections are to be carried out and ensure placement of sub-orders with all required materials, which is mentioned in detail in the following paragraphs. Also, it is vital to have all communications and data entry made clear and to ensure that monitoring of the post-order phase is carried out diligently. We shall explore different challenges faced during post-order. Procurement starts with enquiry and ends with delivery. Hence, until the successful delivery and commissioning of the equipment/package, it is important to track each stage.
First, a quick recap of the stages of the post-order phase:
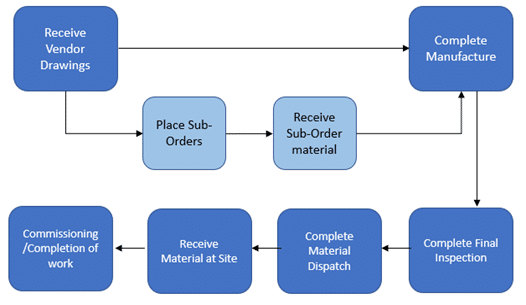
Now let’s look at some of the factors that hinder the progress of procurement during the post-order phase.
Finalizing Vendor Drawings:
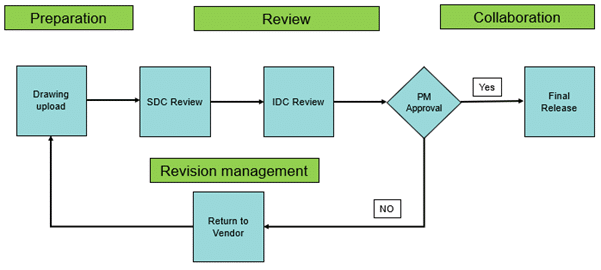
Looking at the typical post-order phase activities, it is evident that we need to minimize the number of changes in finalizing the vendor drawings if we want to have an effective post-order phase which is within the schedule. In order to reduce the number of revisions to the vendor drawing, we can have the comments consolidated and have checkpoints before passing it to the consultant for reviewing the drawing. This can be achieved by using electronic workflows, where, while uploading a drawing, the system prompts you to fill a checklist before submitting it to the consultant. Also, during the stages of review by the consultant’s team, the comments from each team member can be consolidated in a single sheet for the vendor to take necessary actions while re-submitting.
Inspection and Logistics
After receipt of the purchase order from the client, the vendor places sub-orders for procuring materials as per the specifications. The vendor invites the client for inspecting the materials, after approval of which is sent for manufacturing. While carrying put these inspections, it is ensured that procurement of no material is missed out, thus ensuring the availability of equipment along with all materials at the time of delivery to the site. During the manufacturing process, inspections are carried out at various stages. The schedule for inspection must be in line with the project schedule and need to be tracked. It is important to have a record of inspections that were carried out by clients or consultants.
Equipment inspections help in the identification of problems that need to be repaired before they become real and expensive. Digitalized checklists enable the proper maintenance of the data until any period as specified by the client, whereas a manual checklist (on paper) could lead to the displacement of the papers. Also, manipulation of data is not possible on digital checklists as the date of checklist generation, images, points checked, and observations made are all maintained on a real-time basis. Plus, the audit trail of all stages gets captured into the system.
After all the inspections and the completion of all open points, dispatch clearance is obtained. The update at each location during the transit requires to be tracked closely to avoid delays. All required approvals for delivery of the equipment to the site is to be obtained on time in order to adhere to the schedule.
Schedule of Procurement
Managing the procurement cycle timing increases efficiency and procurement costs can be cut by decreasing the cycle times associated with procuring materials and services. Research has found that top performers in procurement take fewer hours to place a purchase order and wait fewer days to receive materials from suppliers.
Reducing procurement cycle time can be carried out by minimizing the time it takes to produce and approve a requisition, get approved purchase orders (PO) into the hands of vendors more quickly, and proactively monitoring open orders. Vendor self-service portals empower vendors to enter their own invoices.
Automating the procurement process with suppliers can significantly reduce the time it takes to receive the ordered product. Automating not only means you receive products needed for key projects sooner, but it can also help increase procure-to-pay efficiency.
Controlled Spending
Uncontrolled spending is one of the toughest challenges faced in procurement. Accidental orders, rush orders, and purchases made outside the company`s established procurement procedures all count as indirect spend, which results in a loss of revenue and control as they cannot be readily accounted for in the company’s financial records. This complicates the procurement strategy, department budgets, inventory management, and financial audits. To ensure that all spend categories are managed as effectively as possible, automating spend management is the best option because it can track complex pricing structures and show exactly where unwanted spending is happening. With all transactions taking place in the same system, it is possible to follow up and ensure there is compliance with the purchasing policy of the organization.
Progress monitoring of procurement
To monitor the progress of procurement, the general practice is to use excel sheets to track the progress of each package based on the tender event schedule. It becomes difficult when there are many packages/materials and the parameters to be tracked increase based on a request from stakeholders involved in the procurement. Also, because you don’t have to show all details to everyone you could end up making multiple spreadsheets in which 75% of the data is the same. Small mistakes and omissions can result in incorrect data, costing you deals, clients, and vendor relationships. Managing your procurement processes manually may appear simple at first but as processes become more complex, they become the largest roadblocks to success.
Avoiding the mistakes of entering the actual status can be controlled by automating the processes through electronic workflows for each stage, where the real-time status is recorded and reflected against the task in each package. The data gets captured in all fields where the input is required, thus avoiding mistakes while entering.
Summing up, while looking at the challenges faced during procurement, irrespective of the pre-order or post-order phase, it is evident how important it is to follow the processes and adhere to the project schedule. However, carrying out all processes manually is time-consuming, and mistakes are bound to happen when the number of bidders or packages is more. Hence digitalization of processes can be a very effective way of handling procurement for any project.
Shabna has over 7+ years of experience in the construction project management sector, having worked with leading consultancies like AECOM, Colliers, and CBRE. She is a Civil Engineer with a Master’s degree in Building Engineering and Management from SPA, New Delhi, and has a deep understanding of project management processes with a focus on project controls and presentation.
Related Posts
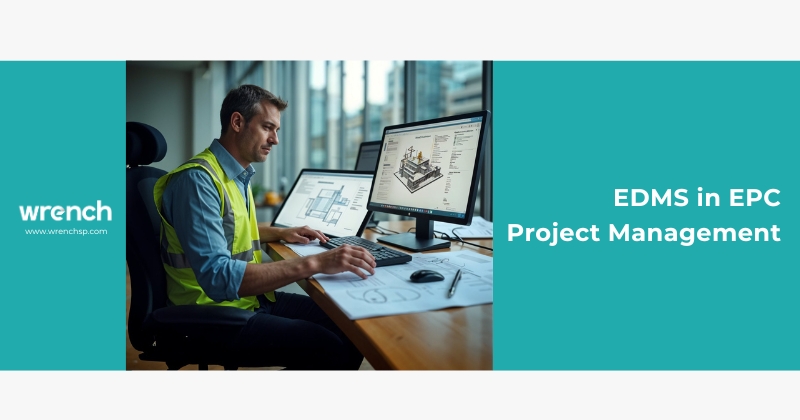
What is an EDMS?
EDMS has become popular in the EPC world in the last decade, especially after the pandemic. What is EDMS? At its core, EDMS is an electronic document management system or a software that organises and…
- 20 Mar 2025
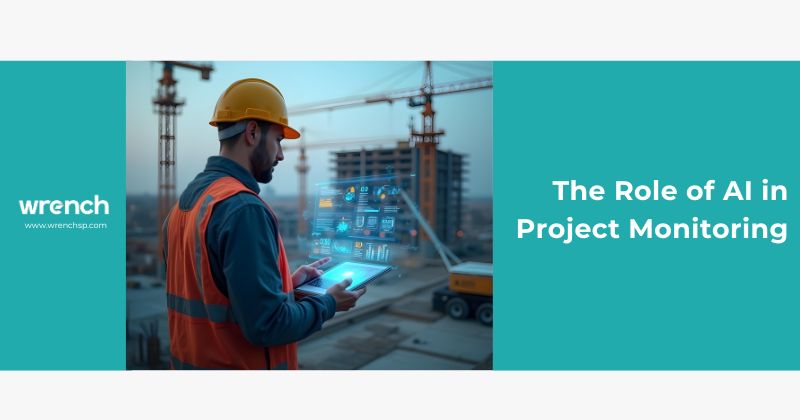
The Role of AI in Project Monitoring
As AI continues to make inroads into every industry in the world and the buzz around it continues to grow, we’re seeing EPC organisations leave behind their historical hesitation about emerging technologies; in fact we’re…
- 13 Mar 2025
Archives
- March 2025
- February 2025
- January 2025
- November 2024
- October 2024
- September 2024
- August 2024
- July 2024
- June 2024
- May 2024
- April 2024
- March 2024
- January 2024
- December 2023
- November 2023
- September 2023
- August 2023
- July 2023
- June 2023
- May 2023
- April 2023
- March 2023
- February 2023
- January 2023
- December 2022
- November 2022
- September 2022
- June 2022
- May 2022
- April 2022
- March 2022
- January 2022
- November 2021
- October 2021
- July 2021
- June 2021
- May 2021
- March 2021
- February 2021
- January 2021
- December 2020
- November 2020
- September 2020
- August 2020
- June 2020
- April 2020
- March 2020
- February 2020
- January 2020
- November 2019
- October 2019
- September 2019
- August 2019
- April 2019
- March 2019
- December 2018
- October 2018
- September 2018
- August 2018
- July 2018
- June 2018
- May 2018
- April 2018
- January 2018
- November 2017
- October 2017
- September 2017
- May 2017
- April 2017
- March 2017
- February 2017
- January 2017